(1) Избор на методи за обработка
Изборът на метода на обработка е да се гарантира точността на обработка и грапавостта на повърхността на обработената повърхност. Тъй като обикновено има много методи за обработка за постигане на едно и също ниво на точност и грапавост на повърхността, е необходимо да се разделят изискванията за формата, размера и топлинната обработка на частите при избора на практика. Например, методите за обработка като скучно, пренасочване и смилане за точни отвори на нивото на IT7 могат да отговарят на изискванията за точност, но дупките в тялото на кутията обикновено използват скучно или пренасочване, вместо да смилат. Като цяло трябва да се избере преиздаване за дребномащабни отвори за кутии, а трябва да се избере скучно, когато диаметърът на отвора е по-голям. Освен това трябва да вземем предвид и търсенето на процент на потребление и икономика, както и практическото положение на потребителското оборудване на фабриката. Точността на икономическата обработка и грапавостта на повърхността на общите методи за обработка могат да бъдат намерени в съответните ръководства за процеса.
(2) Въже владетелят с определен план за обработка
Обработката на сравними прецизни повърхности на части често се постига постепенно чрез груба обработка, полу-завършване и довършителни работи. Не е достатъчно тези повърхности да изберат съответния метод за окончателна обработка въз основа на изискванията за качество и планът за обработка от празната до крайната форма трябва да бъде правилно определен. При определяне на плана за обработка, на първо място, според изискванията на точността и грапавостта на повърхността на първичната повърхност, той трябва да бъде методът на обработка, необходим за достигане на тези изисквания. Например, за дупки с малък диаметър на точността на IT7, когато методът на окончателната обработка е фино пренасочване, той обикновено се обработва чрез пробиване, пренасочване и груба пренапрежение преди финото пренасочване.
Четвърто, разликата между процесите и стъпките
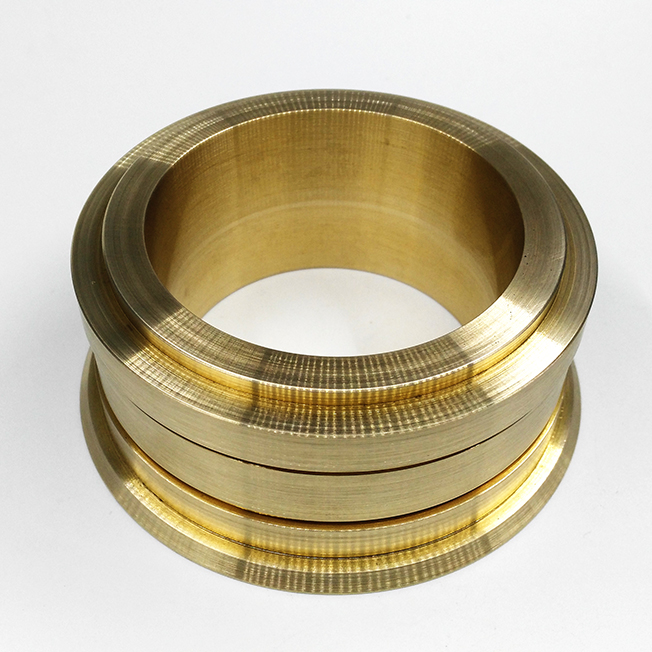
(1) Разграничаването на процеса
Обработването на части на машинен инструмент на ЦПУ може да бъде по -концентрирано в процеса и повечето или всички процеси могат да бъдат завършени колкото е възможно повече в една настройка. На първо място, според чертежа на частта, помислете дали обработената част може да завърши обработката на цялата част върху инструмента за машинно машинно CNC. Ако не, трябва да решите коя част ще бъде обработена на инструмента за машини CNC и коя част ще бъде обработена на други машинни инструменти. Стъпките на обработка на частите са прекратени.
(2) разделението на работните стъпки
Разграничаването на работните стъпки трябва да се разглежда главно от аспектите на точността и мощността на обработката. Често е необходимо да се избират различни инструменти и параметрите на рязане в процеса и да се спират обработката на различни повърхности. За да се улесни анализа и описанието на по -сложния процес, процесът се разделя на стъпки на процеса. Следното приема обработващ център като пример, за да илюстрира владетеля на въжето за стъпки на процеса:
1) Същата повърхност се завършва чрез груба, полу-завършване и завършване на свой ред, или всички преработени повърхности са разделени чрез грубо и довършителни работи.
2) За части както със смилани лица, така и с скучни дупки, лицето може да се смила първо и след това да се скучно. Според този метод за разграничаване на работните стъпки, можете да напреднете в точността на дупката. Поради силата на висока рязане по време на смилането, детайлът е предразположен към деформация. Лицето се смила и след това дупката е отегчена, за да позволи период на възстановяване, за да се намали въздействието върху точността на дупката, причинена от деформацията.
3) Разделете работните стъпки по инструмент. Времето за обръщане на някои машинни инструменти е по -кратко от времето за промяна на инструмента. Можете да изберете да разделите работните стъпки чрез инструмент, за да намалите броя на промените в инструмента и да подобрите мощността на обработката.
Накратко, разграничаването между процесите и стъпките трябва да се разглежда цялостно въз основа на структурните характеристики на специфични части, изисквания за умения и други условия.
Пет, Изборът на оборудване и тела за части
(1) Основният владетел на въжето на устройството за позициониране
1) Стремете се да съответства на показателите за счетоводство за планиране, процес и програмиране.
2) Опитайте се да намалите броя на времето на затягане и да обработите всички повърхности, които да се обработват след позициониране и затягане веднъж, доколкото е възможно.
3) Избягвайте да използвате схеми за обработка на ръчна настройка, които заемат машината, за да дадат пълна игра на ефективността на машинните инструменти на ЦПУ.
(2) Избор на владетел на основното въже на приспособлението
Характеристиките на обработката на ЦПУ дават две основни изисквания за приспособлението: Едното е да се гарантира, че координатната посока на приспособлението е сравнително фиксирана с координатната посока на машинния инструмент; Другото е да се хармонизира връзката на мащаба между частта и координатната система на машинния инструмент. В допълнение, трябва да разгледаме следните четири точки:
1) Когато партидата от части не е голяма, трябва да се използват модулни тела, регулируеми тела и други общи тела, за да се съкрати времето за подготовка на производството и да спести разходите за потребление.
2) Помислете само за използването на специални тела, когато масовата консумация и се стремете да имате проста структура.
3) Зареждането и разтоварването на части трябва да бъде бързо, удобно и надеждно за скъсяване на времето за спиране на машината.
4) Частите на приспособлението не трябва да пречат на обработката на повърхността на частите от машинния инструмент, тоест приспособлението трябва да се отвори и да се позиционира, а компонентите на механизма за затягане не трябва да влияят на рязането по време на обработката (като например неравности и т.н.).
Шест, изборът на инструменти и параметрите на рязане се определя
(1) Избор на инструменти
Изборът на режещи инструменти е едно от важните съдържания в процеса на обработка на ЦПУ. Той не само влияе върху обработващата мощност на машинния инструмент, но и пряко влияе върху качеството на обработката. При програмиране изборът на инструменти обикновено изисква разглеждане на фактори като възможностите за обработка на машинния инструмент, съдържанието на процеса и материала на детайла. В сравнение с традиционните методи за обработка, обработката на ЦПУ има по -високи изисквания за режещи инструменти. Той не само изисква висока точност, добра твърдост и висока издръжливост, но също така изисква стабилни размери и удобни корекции на оборудването. Това изисква използването на нови и висококачествени материали за производство на инструменти за обработка на ЦПУ и оптимизиране на параметрите на инструмента.
При избора на инструмент размерите на инструмента трябва да бъдат съвместими с повърхностните размери и формата на детайла, който ще бъде обработен. В процеса на производство крайните мелници често се използват за обработка на периферните контури на плоски части. Когато фрезирате самолети, трябва да изберете циментиран карбид, поставете фрезови резачки; Когато обработвате шефове и канали, изберете високоскоростни стоманени мелници; Когато обработвате груби повърхности или груби отвори за обработка, можете да изберете циментиран карбид вмъкване на фрезови резачки. Когато избирате крайната мелница за обработка, съответните параметри на инструмента се препоръчват да бъдат избрани според данните за опит. Резачките за фрезоване на топката често се използват за обработка на повърхността, но при обработка на плоски повърхности, резачката се нарязва с горния ръб на топката, а условията за рязане са лоши, така че трябва да се използват резачки за пръстени. В производство на еднократно или малко партида, за да се заменят многокоординираните машинни инструменти за свързване, резачки за барабани или конични резачки, често се използват за обработка на някои променливи части на скосяване на самолета плюс вмъкване на резачки за фреза на зъбите, които са подходящи за CNC машина Инструменти с петосна връзка. За горната обработка на някои сферични повърхности, неговата мощност е почти десет пъти по-висока от тази на резачка за фрезоване на топката и може да се получи добра точност на обработка.
В центъра за обработка различни инструменти се монтират отделно на списанието Tool, а операциите за избор на инструменти и смяна на инструменти се спират по всяко време според правилата на програмата. Следователно е необходимо да има набор от свързващи пръти за свързване на общи инструменти, така че стандартните инструменти, използвани при пробиване, скучно, разширяване, пренасочване, фрезоване и други процеси, могат да бъдат бързо и точно инсталирани в списанието на шпиндела или инструмента на машината инструмент. Като програмист трябва да разберете структурните размери и методите за регулиране на държача на инструмента, използвани на машинния инструмент, и да регулирате скалата, така че радиалните и аксиални размери на инструмента да се определят по време на програмирането. Понастоящем обработващият център на моята страна използва системата TSG East-West, а неговият Shank има два вида: прав Shank (три спецификации) и заострена Shank (четири спецификации), включително общо 16 ножа за различни цели.
(2) Определя се сумата на рязане
Количеството на рязане включва скоростта на шпиндела (скорост на рязане), количеството на рязането на гърба и количеството на подаване. Що се отнася до различни методи за обработка, трябва да се избират различни параметри за рязане и те трябва да бъдат компилирани в списъка на програмата. Разумният подбор на намаляването на ръба на въжето е, че по време на груба обработка, процентът на потребление напред обикновено е основният фактор, но трябва да се вземат предвид и разходите за икономика и обработка; Полузарязването и довършването трябва да бъдат координирани с предположението за осигуряване на качествената енергия, икономика и разходи за обработка. Специфичната стойност трябва да се определя в съответствие с ръководството за машинен инструмент, ръководството за параметър за рязане и отделен опит.
Седем, точката за настройка на инструмента и точката за промяна на инструмента са определени
Когато програмирате, трябва правилно да изберете ориентацията на „точка на настройка на инструмента“ и „точка за промяна на инструмента“. "Точката за настройка на инструмента" е отправна точка на инструмента спрямо движението на детайла при обработване на части върху инструмента за машинно CNC. Тъй като програмният сегмент първоначално се изпълнява от този момент, точката на настройка на инструмента също се нарича „Програма Начална точка“ или „Начална точка на инструмента“.
Владетелят на въжето за избор на точката на ножа е:
1. Улесняване на използването на цифрова обработка и опростяване на програмирането;
2. Лесно е да се подравнява върху машинния инструмент и лесно да се провери по време на обработката;
3. причинената грешка в обработката е малка.
Точката за настройка на инструмента може да бъде избрана на детайла или от външната страна на детайла (например върху приспособлението или върху машинния инструмент), но тя трябва да има определена връзка с размерите с датата на позициониране на частта. За да се подобри точността на обработка, точката на настройка на инструмента трябва да бъде избрана, доколкото е възможно при справка за планиране или справка за процеса на частта, като детайла, разположена от дупката, центърът на дупката може да бъде избран като инструмент точка на настройка. Ориентацията на инструмента е приведена в съответствие с този отвор, така че „точка на позицията на инструмента“ и „точката на настройка на инструмента“ съвпадат. Общият метод за калибриране във фабриките е да инсталирате индикатора за набиране на шпиндела на машинния инструмент и след това да разточите шпиндела на машинния инструмент, за да направите "позицията на позицията на инструмента" различна от точката на настройка на инструмента. Колкото по -добра е несъвместимостта, толкова по -голяма е точността на настройката на инструмента. Така наречената „точка на местоположението на инструмента“ се отнася до върха на инструмента за завъртане и скучен инструмент; върхът на тренировка; Центърът на долната повърхност на крайната мелница и главата на мелницата и центърът на края на топката на мелницата на топката. След частите и оборудването, координираната система на детайла и координатната система на машинния инструмент имат определена мащабна връзка. След като е зададена координатната система на детайла, първоначалната стойност на координатите на първия блок от точката на настройка на инструмента; Стойността на координатата на точката на настройка на инструмента в системата на координатата на машинния инструмент е (x0, y0). Когато програмирането по абсолютна стойност, независимо дали точката на настройка на инструмента и произходът на детайла могат да съвпадат, те са X2 и Y2; Когато програмирането по инкрементална стойност, когато точката на настройка на инструмента съвпада с произхода на детайла, координатната стойност на първия блок е, когато X2 и Y2 не се припокриват, тя е (x1 + x2), y1 + y2). Точката за настройка на инструмента е не само началото на програмата, но и края на програмата. Следователно е необходимо да се разгледа многократната точност на точката на настройка на инструмента в производството на партиди. Точността може да бъде проверена от стойността на координатата (x0, y0) на точката на настройка на инструмента далеч от произхода на машината. Така нареченият "Машинен произход" се отнася до фиксирана гранична точка на машинния инструмент. Например, за струг, той се отнася до точката на пресичане между центъра на обръщане на основния вал на струг и крайното лице на главата на Чък. Когато инструментът трябва да бъде променен по време на процеса на обработка, точката на промяна на инструмента трябва да бъде решена. Така наречената „точка за промяна на инструмента“ е ориентацията на държача на инструмента, когато той е индексиран и променен. Тази точка може да бъде фиксирана точка (като машинен инструмент за обработен център, ориентацията на манипулатора за промяна на инструмента е фиксирана) или произволна точка (като струг). Точката за промяна на инструмента трябва да бъде разположена извън детайла или приспособлението, а държачът на инструмента не докосва детайла или други части, когато е индексиран. Зададената стойност може да бъде определена чрез практически методи за измерване или счетоводство.
8. Определено се определя маршрутът за обработка
При обработката на ЦПУ пътят на позицията на инструмента, свързан с движението на детайла, се нарича обработващ път. При програмиране има следните точки за определяне на дължината на маршрута за обработка:
1) Пътят на обработка трябва да гарантира точността и грапавостта на повърхността на обработените части и мощността трябва да бъде висока.
2) Направете численото изчисление лесно, за да намалите количеството на програмирането.
3) Пътят на обработка трябва да бъде най -краткият, така че да може да намали програмния сегмент и времето на празния инструмент. В случай на степен и т.н., това трябва да е единичен пропуск или множество пропуски за завършване на обработката и в процеса на смилане, независимо дали да изберете смилане или нарязано фрезоване и т.н.
За контролирани с точкова машина CNC машини са необходими само висока точност на позициониране, а процесът на позициониране е възможно най-бърз, а пътят на движение на инструмента спрямо детайла е без значение. Следователно такива машинни инструменти трябва да подреждат пътя на инструмента според най -краткото разстояние на празен ход. В допълнение, трябва да се определи аксиалното движение на движението. Размерът се определя главно от дълбочината на отвора на обработената част, но трябва да се вземат предвид и някои спомагателни скали, като например разстоянието на въвеждане и превишеното количество на инструмента.